Plywood is spliced with log veneers and then pasted with glue. Different quality plywood can be distinguished according to the type of wood and the grade of glue. Let me introduce to you the general production process of plywood.
Plywood production process: veneer finishing → bonding molding → pre-pressing → hot pressing → cutting → sanding → inspection and grading → packaging and storage.
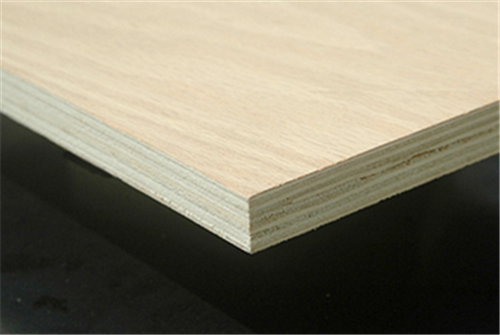
- Log sawing: The length of imported logs is generally more than 6 meters. It should be sawed according to the length and quality required by the process. The cut wood should be the length of the finished plywood plus a machining allowance. For example, a piece of finished plywood with a width of 1220mmX2440mm, the length of the wood segment is usually 2600mm or 1300mm. The length of the log and the curvature and defects of the log directly affect the yield of plywood. The waste generated includes small wood chips, chips and sawdust. The sawing loss rate of logs is generally 3-10%.

- Veneer rotary cutting: The most widely used plywood production is the veneer produced by rotary cutting. The loss in this process is the greatest. First, a considerable part of the veneer of the cross-section cannot be used because the wood segment is not round; second, the end loss is caused by the rotary cutter clamped at both ends of the wood segment; third, the wood core loss. The waste from veneer stripping is shredded veneer and wood core. It can be seen that the loss of veneer peeling is related to the material, diameter and equipment performance of the wood segment, and the loss rate of this part is 15% to 25%.
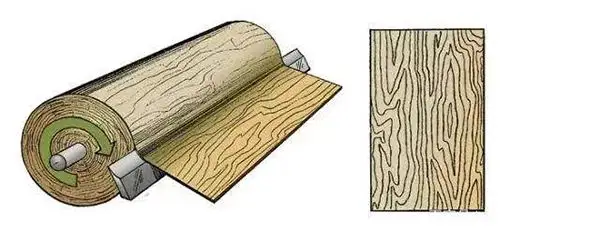
- Veneer drying: The moisture content of the veneer after rotary cutting is very high, and the veneer must be dried to meet the requirements of the gluing process. When wood dries, the dimensions become smaller, which is called drying shrinkage. The length, width and thickness of the veneer shrink with decreasing moisture content. The shrinkage loss is related to the tree species of the veneer, the moisture content of the veneer and the thickness of the veneer. The drying shrinkage rate is generally 4% to 10%.

- Veneer finishing: Veneer finishing includes cutting, assembly and repair. The dried strip veneer and sheet veneer are cut into specification veneer and splicable veneer, the narrow veneer is spliced into a whole veneer, and the defective whole veneer is repaired to realize the technological process. Quality requirements. The amount of waste veneer produced in this process is related to factors such as the material of the log, the quality of the rotary veneer, the quality of the dried veneer, and the operator’s familiarity with the veneer standard. The loss rate is generally 4% to 16%. .The process loss rate of imported veneer directly processed into plywood is generally 2%~11%.

- Hot pressing: The floors that have been painted are firmly bonded together by a certain temperature and a certain pressure. During hot pressing, as the temperature and moisture content of the slab change, the wood is gradually compressed, and the thickness of the slab gradually decreases. This loss is the compression loss, which is related to the hot pressing temperature, unit pressure, hot pressing time, tree species and moisture content of the plywood. The loss rate is generally 3% to 8%.
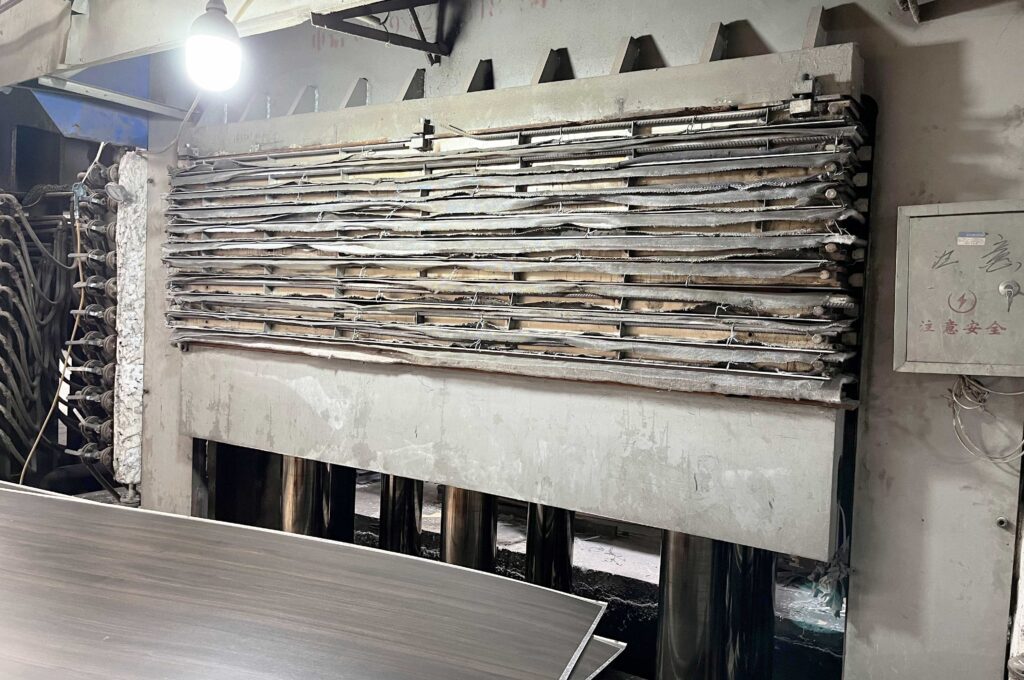
- Trimming: Cut the hot-pressed board into specification boards. The amount of trimming waste is related to the machining allowance and width of the plywood. The larger the width of the plywood, the smaller the cutting edge loss rate, generally 6% to 9%.

Sanding: Sand the surface of the plywood to make the surface smooth and beautiful. The waste produced in this process is sanding powder. When the quality of the veneer is good, the polishing amount is small, and the polishing loss rate is generally 2% to 6%.
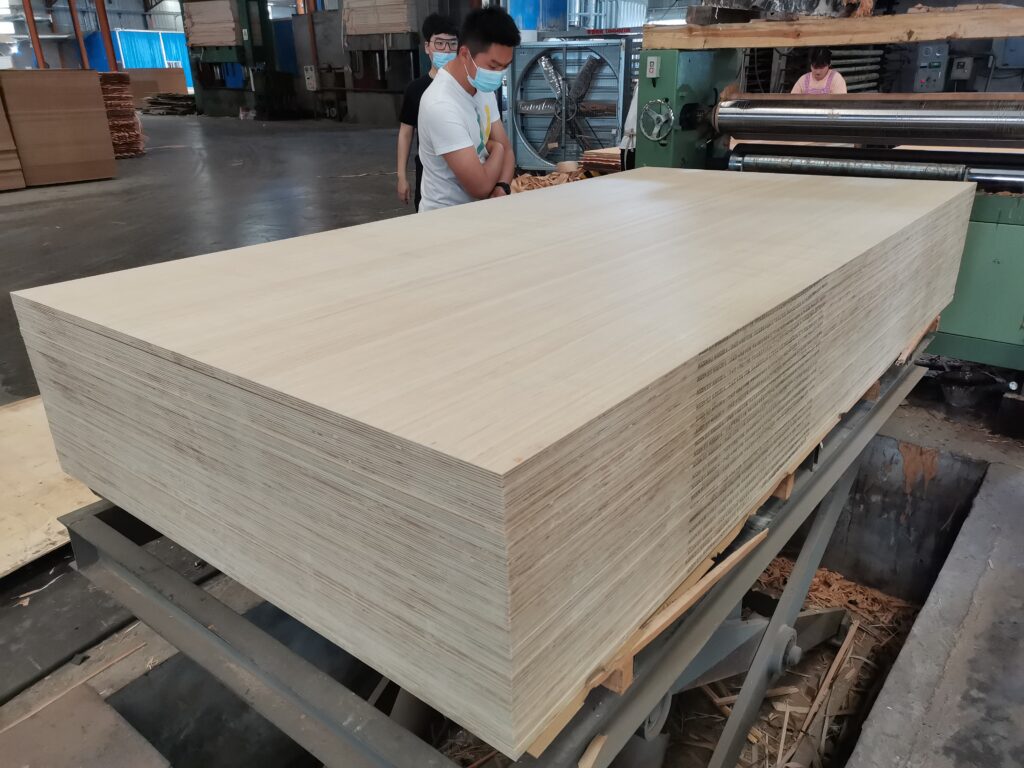
Finished product, packing, loading and dispatching
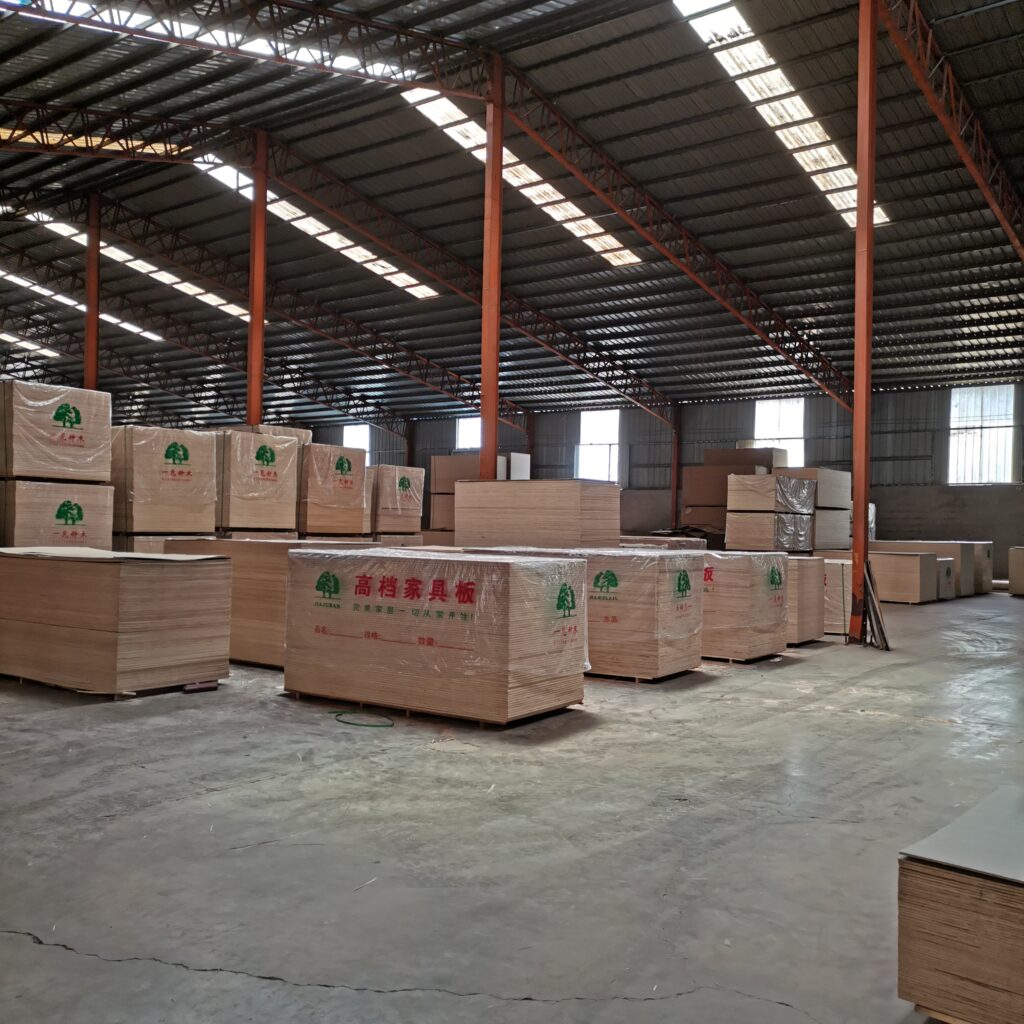